Extending the Service Life of Electric Motors
How screened cables can reduce harmful bearing currents
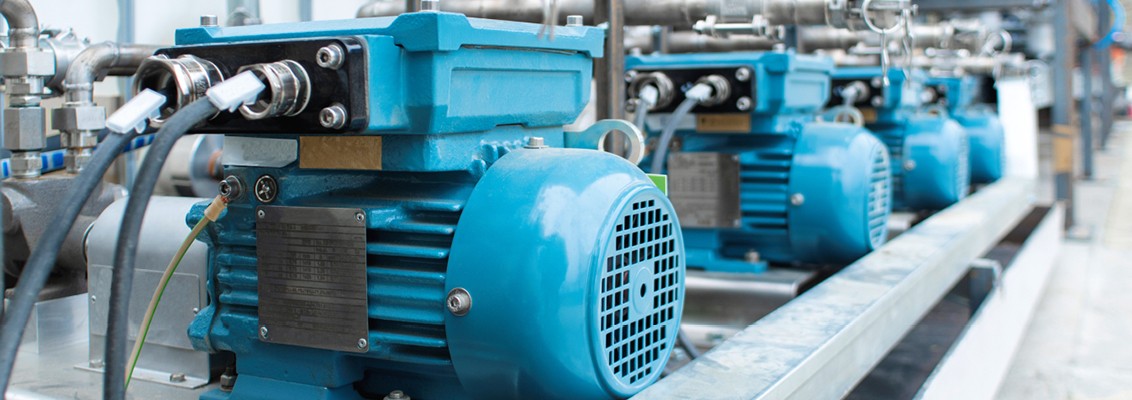
When operating electric motors with frequency converters, undesirable bearing currents often occur which can significantly impact the service life of the rolling contact bearings. Scientists at TU Darmstadt have investigated these bearing currents - and found out that they can be reduced in some cases with the help of screened motor supply cables.
Bearing currents are undesirable currents that occur during the operation of electric motors. They flow through the roller bearings that connect the movable rotor to the fixed motor stator. Bearing currents occur mainly in drives where the speed is changed with the help of a frequency converter and can cause considerable damage to the bearings. Particularly in cases that have an inappropriate earthing concept, bearing currents with high current densities can occur, which melt or even steam the metal in the bearing ring. The result is craters and so-called riffles in the roller bearing, which become noticeable with increased vibrations and even faster wear. As a result, the bearing often fails only a few months after installation.
There are four kinds of bearing currents, each of which is influenced by different factors and has varying degrees of impact:
- Capacitive bearing currents are caused by the voltage across the bearing changing and compensating the currents flowing. These are typically too small to be harmful.
- Discharge bearing currents (EDM) are pulsed discharge currents. They can occur if the voltage increases in the bearing across the lubricant film until it is electrically broken.
- Circular bearing currents are circular currents in the electrical machine. This is caused by a high-frequency magnetic ring flux around the shaft, which induces a voltage along the shaft.
- Rotor-to-earth bearing currents can occur if the rotor of the electric drive is additionally earthed through a gearbox or another device and its earth impedance is lower than that of the stator. The current flows proportionally from the motor housing through the bearings into the shaft and across the earth connection of the rotor.
However, by designing the bearing appropriately, using hybrid or ceramic bearings as well as brushes, filters and earthing rings, design engineers have some options to reduce and avoid these unwanted currents.
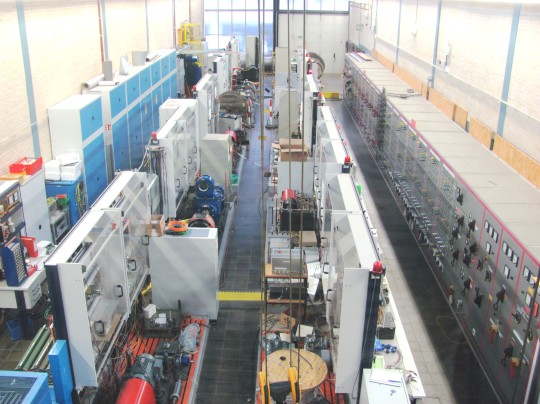
Screening Makes the Difference
A decisive criterion is the selection of the right motor cable - this was the result of a study by the Institute for Electrical Energy Conversion at the Technical University of Darmstadt, carried out with the cooperation of HELUKABEL. The scientists compared the occurring bearing currents for cable types with and without screening in several test setups. In the process, they found out that rotor-to-earth bearing currents in particular can be significantly reduced by using screened cables.
Screened cables are a simple and effective method to protect rolling-contact bearings from premature wear and failure. An additional advantage: their screening also prevents unwanted electrical radiation to other devices and thus contributes to the electromagnetic compatibility (EMC) of the entire system.
In its tests, the team from the TU Darmstadt used HELUKABEL motor cables of the type TOPFLEX-EMV-UV-3 PLUS 2YSLCYK-J . This double-screened cable is designed for interference-free operation of frequency converters. Furthermore, it is UV and weather resistant and therefore suitable for outdoor use. HELUKABEL offers its TOPFLEX series in many versions according to different requirements - and has an extensive range of servo and feedback cables for industry and mechanical engineering.
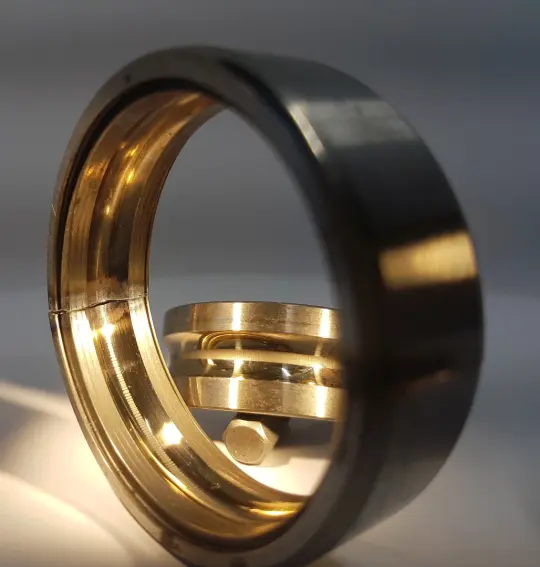