How Cables Are Made – Step 4: Laying Up
In the fourth part of our series, you will learn how and why we strand single cores together.
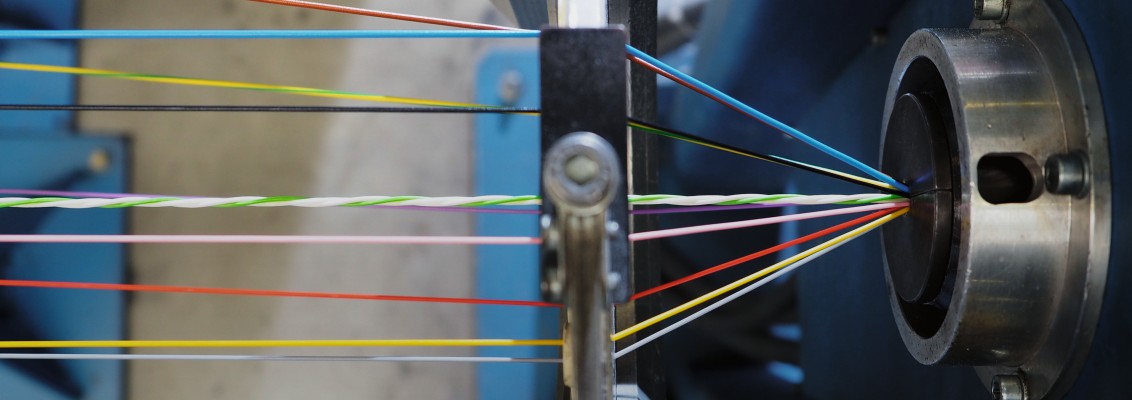
Read the previous production steps:
After insulation, the next step in the process is to strand the single cores together, i.e. to mechanically twist them together in accordance with predefined geometric specifications to reduce the mutual interference between the electrical conductors caused by magnetic coupling. Stranding the cores together also serves another purpose: it ensures that the finished product is mechanically robust and flexible.
In practice, cores can be stranded together in different ways, but pair twisting is the simplest. As its name suggests, this involves twisting two single cores into a pair, and is typically used in network or telephone cables . The stranded cores can subsequently be twisted together. Seven equally thick elements can form a concentric circular construction; with higher numbers, the pairs are stranded in layers. For cables that have to withstand high mechanical stresses and movements, bundle stranding is recommended. This involves twisting several bundles of single cores into one main bundle. Stranding in bundles causes all cores to change their inner and outer radius several times over a fixed distance in the bent cable. As a result, the tensile and compressive forces balance each other out.
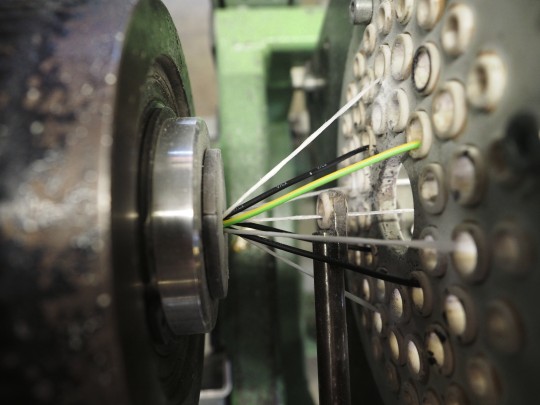
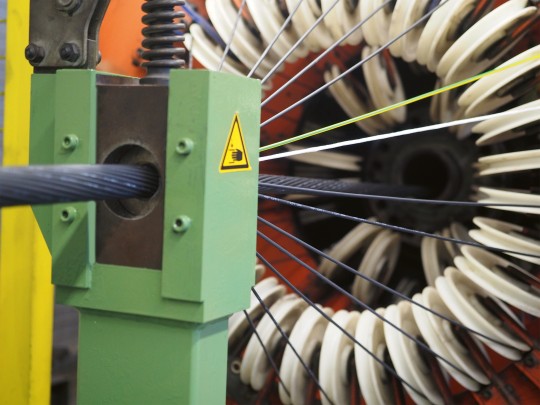
What is the lay length?
An important measure during stranding is the lay length. It is defined as the length of a single stranding element when it is fully rotated about its axis. For example, a lay length of 70 mm (2.75 in) means each conductor makes a helical rotation of 360 degrees around the strand axis every 70 mm. The shorter the lay length, the more flexible the cable. The lay length also determines the amount of material used. The individual cores must be longer than the finished cable as the stranding process shortens the cable; the shorter the lay length, the higher the contraction factor.
Ask the Expert
Mr. Schmidt, why are additional filler materials inserted between conductors during cable production?
Filler materials have several functions: first, they are used to shape the cable, i.e. to make it round. They also increase stability by ensuring that the cable cross section does not contain any cavities. The filler can be placed directly in the centre of the cable or around it. The former is referred to as the core or core filler. Fillers are non-conductive and usually made from polypropylene.
What does stranding with backtwist mean?
High-quality cables in moving or permanently moving applications, i.e. in drag chains or robots, are stranded with a backtwist. This procedure involves using the unwinding units in the special stranding machines to apply a twist in the opposite direction to the stranding direction to neutralise twisting in the conductors and hence make the stranded bond as torsion-free as possible.
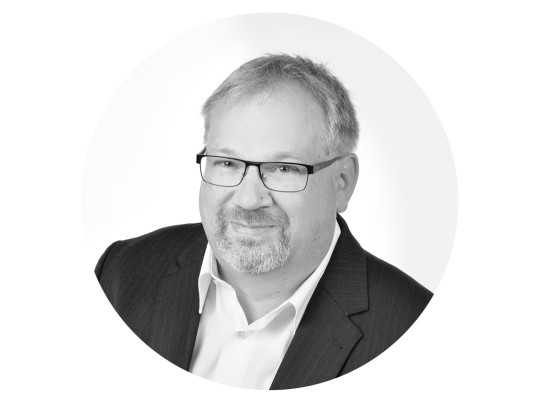
Would you like even more insights? Discover our test laboratory series and the various test procedures.