So entstehen Kabel – Schritt 3: Die Aderisolation
Im dritten Teil unserer Serie erfahren Sie, wie wir Kupferlitzen mit Kunststoffen isolieren.
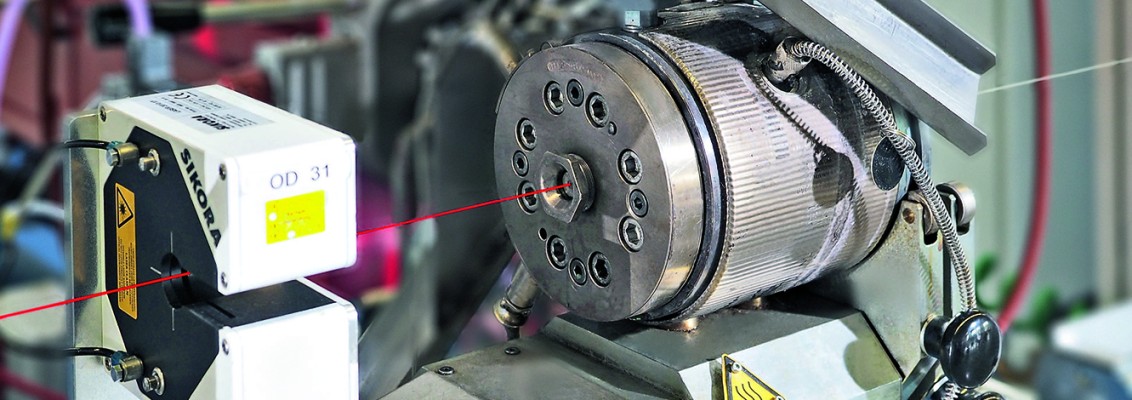
Lesen Sie auch die vorangegangenen Produktionsschritte:
Auf das Verlitzen der Einzeldrähte zu einem Leiter folgt im nächsten Schritt dessen Isolation. Die sogenannte Aderisolation schützt den blanken Litzenleiter und vermeidet Kurzschlüsse innerhalb des Kabels. Als Isoliermaterial kommen in der Regel Kunststoffe zum Einsatz. Aus dem Bereich der Thermoplaste werden am häufigsten Polyvinylchlorid (PVC), Polyethylen (PE) und Polypropylen (PP) verwendet.
Jeder Isolierstoff kann nur bis zu einer gewissen Spannung und Temperatur isolieren. PVC eignet sich für die meisten Standardleitungen. Sind höhere Temperaturen zum Beispiel bei Motoranschlussleitungen oder eine höhere Spannungsfestigkeit gefragt, fällt die Wahl auf PP oder den vernetzten Kunststoff XLPE. Bei Datenkabeln ist es wichtig, dass der Verlustfaktor möglichst gering ist, aufgrund seiner Eigenschaften eignet sich daher PE als Isolierwerkstoff. Je nach Anforderung an das Kabel werden zur Isolation auch die Elastomere Gummi und Silikon eingesetzt, die im Vergleich zu den Thermoplasten thermisch robuster sind.
Die Kunststoffgranulate werden im Extruder geschmolzen und um den Leiter gespritzt. Elektrische Anforderungen an das Kabel wie zum Beispiel die Spannungsfestigkeit bestimmen die Mindestwanddicke der Isolierschicht. Hierbei ist es besonders wichtig, dass diese den Leiter gleichmäßig dick umhüllt. Ansonsten hätten Abschnitte, wo die Mindestisolierwanddicke unterschritten wird, eine zu geringe Spannungsfestigkeit und es kommt zu Kurzschlüssen.
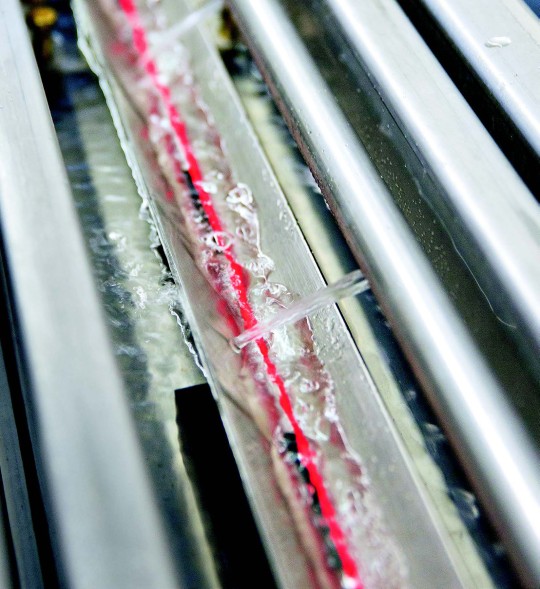
Aderkennzeichnung
Für eine klare Zuordnung der Adern an beiden Kabelenden werden die Adern durch Farben, Ziffern oder andere Aufdrucke gekennzeichnet. Die Kennzeichnung erfolgt in der Regel nach nationalen oder internationalen Normen. Das sorgt für vergleichbare Produkte. Niederspannungskabel und -leitungen werden nach DIN VDE 0293-308 häufig farb-codiert. Den Aderfarben sind dabei bestimmte Funktionen zugeordnet:
- Außenleiter: braun, schwarz, grau
- Neutralleiter: blau
- Schutzleiter: grün-gelb
Fragen an den Experten
Für die Qualität der Leitung ist eine gleichmäßig dicke Isolierschicht ausschlaggebend. Wie wird diese gewährleistet?
Der Leiter muss hierbei absolut mittig positioniert sein und während des gesamten Extrusionsprozesses auch bleiben. Deshalb ist es so wichtig, dass bei der Aderisolation nur Präzisionswerkzeuge zum Einsatz kommen. Die Spritzdüsen des Extruders beispielsweise müssen exakt gearbeitet sein und dürfen nahezu keinen Toleranzbereich aufweisen.
Warum sollte die Isolierschicht möglichst dünn sein?
Jeder möchte später ein Kabel haben, das kostengünstig, platzsparend und leicht ist. Daher wird bereits bei der Isolation der einzelnen Leiter darauf geachtet, die Isolierschicht möglichst dünn zu halten. Bei HELUKABEL misst ein Laser während der Extrusion des Kunststoffs den genauen Außendurchmesser. Bei Bedarf kann der Extruder automatisch innerhalb eines Grenzwertbereichs nachregeln. Dennoch werden Stichproben aus jedem einzelnen Produktionsschritt entnommen und genauen Qualitätskontrollen unter dem Mikroskop unterzogen.
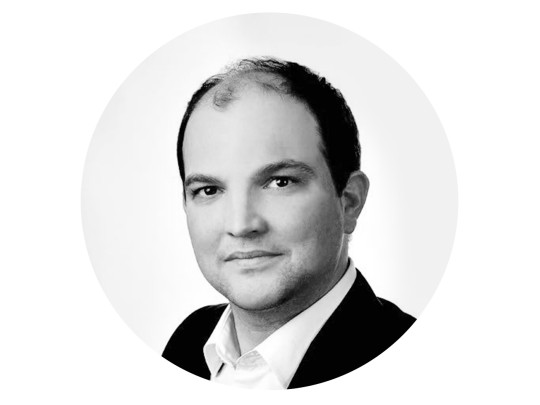