So entstehen Kabel – Schritt 6: Die Mantelextrusion
Im sechsten Teil unserer Serie erfahren Sie, wie der Mantel aufgebracht wird.
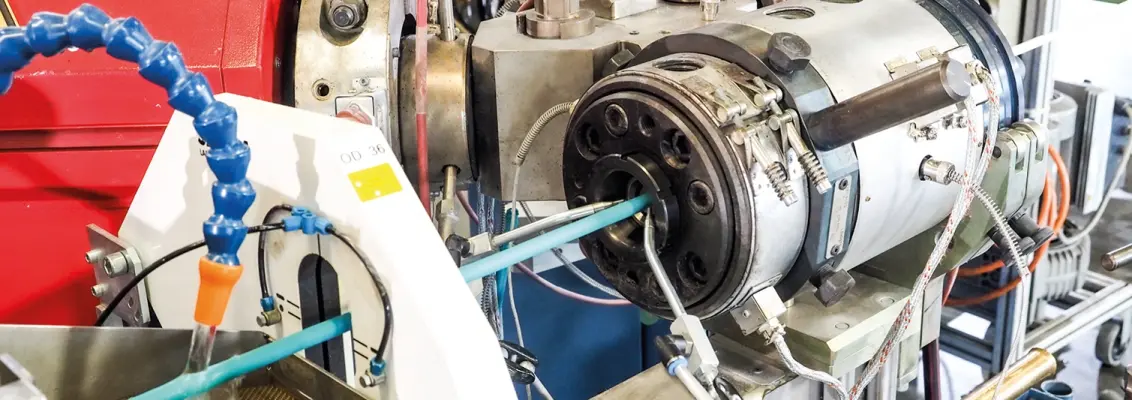
Lesen Sie auch die vorangegangenen Produktionsschritte:
Die Mantelextrusion
Verseilungen aus mehreren Einzeladern – ob mit oder ohne zusätzliches Geflecht – benötigen einen Mantel. Erst dieser macht aus den verschiedenen Komponenten ein komplettes Kabel. Zweck der Ummantelung ist aber nicht nur der Zusammenhalt der darin enthaltenen Adern, Geflechts- und Füllmaterialien. Sie schützt das Kabel auch bei mechanischen Belastungen wie Biegung und Torsion und macht es beständig gegen Hitze, Kälte, Feuer, Chemikalien, Wasser oder Öl.
Um die speziellen Herausforderungen der jeweiligen Anwendung optimal zu erfüllen, muss aus einer Vielzahl von Mantelmaterialien das jeweils passende ausgewählt werden.
HELUKABEL verarbeitet in seinen Produktionswerken mehr als 80 verschiedene Kunststoffe.
Die gängigsten davon sind:
- Polyvinylchlorid (PVC): Dieser Kunststoff überzeugt durch niedrige Kosten und allgemeine chemische Beständigkeit. PVC ist jedoch mechanisch nur bedingt belastbar und standardmäßig nicht ölbeständig.
- Polyurethan (PUR): Hochwertiger und abriebfester Kunststoff, beständig gegen Öl und Chemikalien, geeignet für dynamische Anwendungen.
- Thermoplastische Elastomere (TPE): Diese widerstandsfähigen Kunststoffe eignen sich etwa für hohe mechanische Belastungen und für den Einsatz in feuchten und nassen Räumen.
Die Wandstärken des Mantels können dabei zwischen 0,2 und 5 Millimetern betragen, liegen aber in der Regel bei 0,8 bis 1,2 Millimetern. Die dünnsten bei HELUKABEL gefertigten Mantelleitungen haben einen Durchmesser von gerade einmal 2,4 Millimetern, die dicksten stolze 78 Millimeter.
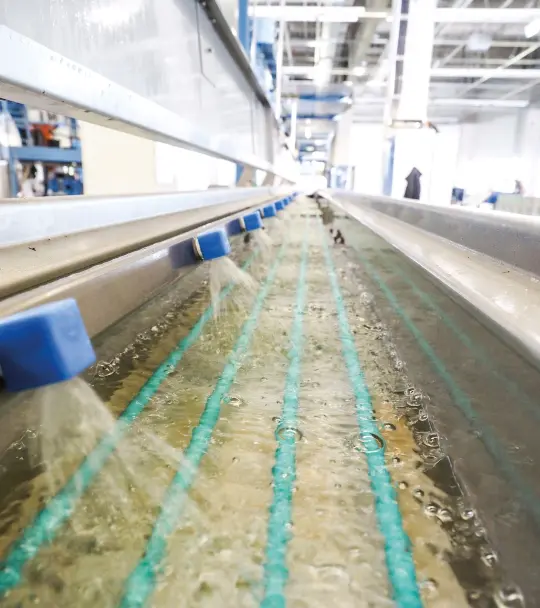
Genau wie bei der Aderisolation wird der Mantel mit einem Extruder aufgebracht. Dieser besteht aus einer Dosiereinheit für das Kunststoffgranulat, einer Schnecke, die das Material transportiert und erwärmt, sowie einem Zylinder mit Spritzkopf, der den zähflüssigen Kunststoff gleichmäßig auf das durchlaufende Kabel aufträgt. Anschließend läuft das Kabel durch ein Wasserbad, wo der Mantel abkühlt und aushärtet (siehe Bild). Das ummantelte Kabel wird mit Laserkameras und Hochspannungstestern geprüft und zu guter Letzt aufgewickelt, bevor es zum finalen Fertigungsschritt gelangt: der Kennzeichnung.
Fragen an den Experten
Herr Sefünc, worin besteht der Unterschied zwischen Aderisolation und Mantel?
Ganz einfach: Die Aderisolation hat die Aufgabe, in mehradrigen Leitungen die einzelnen Elemente galvanisch voneinander zu trennen. Sie wird daher auf jede Ader einzeln aufgebracht und beeinflusst die elektrischen Eigenschaften eines Kabels wie etwa die Spannungsfestigkeit. Der Mantel hingegen schützt das Innenleben eines Kabels vor schädlichen Umwelteinflüssen sowie bei mechanischer Belastung. Er hat keine elektrische Funktion. Der Herstellungsprozess ist jedoch derselbe: Bei beiden handelt es sich um eine dünne Schicht Kunststoff, die mit einem Extruder aufgetragen wird.
Welche Faktoren gilt es bei der Mantelextrusion zu beachten?
Da spielen viele Parameter eine Rolle: etwa der Durchmesser des Kabels selbst. Denn je dicker die Leitung, desto stärker muss auch der Mantel sein, damit sie allen Belastungen standhält. Und natürlich muss die Wandstärke möglichst gleichmäßig und konzentrisch sein, um eine harmonische Funktion und maschinelle Verarbeitbarkeit des Kabels sicherzustellen, zum Beispiel beim Abmanteln.
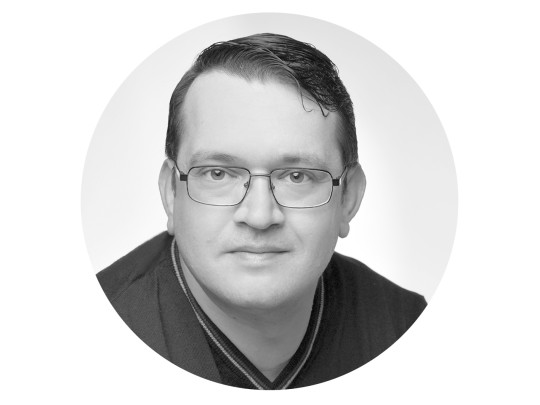
Wie bekommen die Kabel eigentlich ihre jeweilige Farbe?
Das Farbstoffkonzentrat im gewünschten Farbton wird im Dosiergerät des Extruders dem Kunststoffgranulat beigemischt. In der Schnecke entsteht daraus unter Wärmeeinfluss eine homogene und zähflüssige Masse, ähnlich wie Honig. Die wird über einen Spritzkopf aufgetragen, so dass das Kabel am Ende in der vom Kunden georderten Farbe aus der Maschine kommt. Es sind fast alle erdenklichen RAL-Töne möglich. Für einige Werkstoffe müssen spezielle Farbbatches hergestellt werden.